Definition:
Pump is a device which moves fluid from one location to another by means of suction or pressure.
Types of pumps:
“Pumps are primarily classified into two categories according to the principal of energy addition”.
One is kinetic pumps where energy is continuously added to the liquid to increase its velocity. Subsequently the velocity is reduced which increases the pressure of liquid.
The other one is Positive displacement pump where energy is added periodically by direct application of force to one or more movable volumes of liquid. This direct application of force increases the pressure of liquid to a value required to move through the ports in discharge line.
Below is a broad classification of types of pumps.
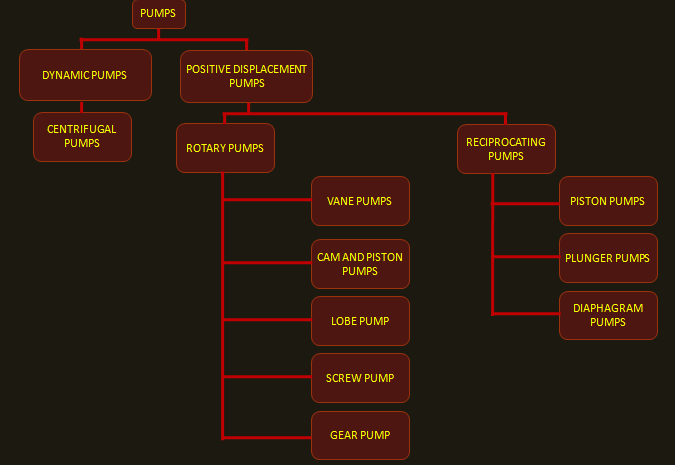
Please note -There are many pumps available which have working principle other than these mentioned below but are not covered here, as they are used rarely or used in special condition in process application.
In this post we will discuss about the reciprocating and rotary pumps. These are positive displacement pumps which mean a set volume of fluid is discharged for each complete rotation of shaft.
“Api standard-674 specifies the requirements for Reciprocating pumps for use in oil and gas industries”
Reciprocating pumps:
In these types of pumps the commodity fills the suction chamber when the plunger or piston draws back and when the plunger/piston moves forward it pushes the fluid into discharge nozzle with higher pressure.
It is used where a precise amount of fluid is required to be delivered, inject small amount of additives in high pressure systems and where the delivery pressure required is higher than can be achieved with other types.
These pumps discharge a definite quantity of liquid during piston or plunger through the stroke distance. Characterised by pulsating flow in both suction and discharge line hold down supports are recommended for effective length.
Reciprocating pumps can further be divided into three types as mentioned below.
1. Piston pumps:
Piston pumps are used when medium to high delivery pressure is required Such as high pressure flushing of vessel interiors. It is also used in Relative high pressure service with an abrasive liquid. Reciprocating piston pumps are considered batter in abrasive application than plunger pumps.
Piston pumps have relatively slower speeds than plunger pumps which makes them relatively lower in maintenance expense and longer life than plunger pumps. Often this type comes with multi cylinder form and can be single or double acting. piston pumps commonly available in axial and radial design type . working animation for axial piston pump is provided in below
2. Plunger pumps:
In a plunger pump the reciprocating member is a plunger instead of a piston. To tell the difference between a piston and plunger-A piston usually has a high pressure seal around it which reciprocates inside a smooth cylinder where as plunger is a smooth cylinder which reciprocates inside a cylindrical stationary seal.
Plunger pumps are used in high pressure application than piston pumps, in metering applications and proportionality of fluids. In these types pressure up to 50,000psi is achieved which is highest pressure obtainable among positive displacement pumps.
2. Diaphragm pumps:
Diaphragm pumps are similar to piston and plunger pumps except that the reciprocating action of the pump causes a Diaphragm to flex back and forth, which in turns causes the liquid to flow into and out of the pump. This diaphragm is usually made of an elastic material which allows it to flex.
In diaphragm pumps no seals or packing is exposed to the liquid being pumped which makes them idle for handling hazardous or toxic liquid.
A simple comparison between the working of the above 3 types of pumps is provided in below figure.

Rotary pumps:
“Api standard-676 specifies the requirements for Rotary pumps for use in oil and gas industries”
Here liquid is drawn into suction nozzle through a set of gear and screws. When the gear and screws rotate the fluid is filled into the space between them and further rotation of the gear and screws pushes the fluid out through the discharge nozzle.
This is used for high viscous fluids like grease, heavy fuel oil, molasses, lube oils etc. unlike reciprocating flow where there is a pulsating fluid flow in rotary pumps the flow is smooth.
Some commonly used rotary pump types are mentioned below.
1. Screw pump.
Screw pumps are used to pump heavy viscous fluid and non abrasive slurries and sludge
2. Gear type pumps
Gear pumps are used to pump oils and non abrasive fluids.
3. Lobe pumps
Rotary lobe pumps are non-contacting and have large pumping chambers, allowing them to handle solid food products. They are also used to handle slurries, pastes, and a wide variety of other liquids
4. Vane pump
Vane pumps are mainly used in auto industries as high pressure hydraulic pumps for transferring fuels, lubes, refrigeration coolants and also used for Lpg cylinder filling
Working principle of all above mentioned pumps are well explained in below video link.
Leave a Reply